Drum brake forging has rapidly evolved into a vital component in the automotive and manufacturing industries due to its durability and reliability. Drawing on decades of experience in the field, the importance of expertise, authoritativeness, and trustworthiness becomes increasingly apparent when discussing drum brake forge processes.

The process of creating a drum brake through forging is more than just a manufacturing technique; it's a symphony of metallurgy and precision engineering. Unlike other methods, forging involves heating and shaping metal to produce components of superior strength. This method ensures that the drum brake can withstand significant forces without failing, making it indispensable for high-stress applications such as heavy trucks and industrial machinery.
One professional aspect to consider in drum brake forging is the selection of materials. High-grade steels and alloys are typically chosen for their excellent strength-to-weight ratios and resistance to wear and tear. The material's quality directly impacts the lifespan and efficacy of the brake, emphasizing the need for authoritative sources and expert consultations to ensure the correct alloy is selected.
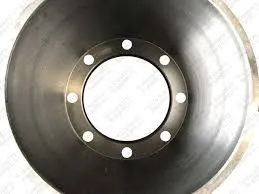
The expertise involved in adjusting the forging process according to the specific material properties cannot be understated. The heating temperature, die design, and cooling methods are all tailored to optimize the grain structure of the metal. This customization enhances the mechanical properties of the finished drum brake, providing an edge over components produced by lesser manufacturing techniques.
A crucial consideration for improving experience and trustworthiness in the product is the precision machining that follows forging. After the initial forging process, the drum brake undergoes various machining operations to achieve exact dimensions and balance. This phase underscores the importance of skilled machinists and advanced CNC machines to achieve the tight tolerances required for seamless braking performance.
Experts highlight the significance of rigorous testing and quality assurance processes in drum brake production. Each brake must undergo stringent checks to identify any potential defects or deviations from the desired specifications. Non-destructive testing methods, such as magnetic particle inspection and ultrasonic testing, are employed to ensure the structural integrity of each component.
drum brake forge
As a hallmark of trust and reliability, companies involved in drum brake forging often pursue certifications and adherence to international standards. ISO 9001 and IATF 16949 certifications serve as a testament to a company's commitment to quality management and continuous improvement. These credentials provide customers confidence in the product's quality, establishing a reputation for dependability in the marketplace.
In terms of authoritativeness, partnering with established industry leaders for drum brake components further hones a company's competitive edge. Large-scale manufacturers not only benefit from economies of scale but also from exclusive access to the latest technological advancements and industry insights. Collaborations with such entities ensure that the drum brakes produced meet and exceed global performance standards, aligning with the expectations of modern consumers and OEMs alike.
Innovative developments in the drum brake forge sector are continually enhancing product performance and broadening application possibilities. Technological advancements such as computer-aided design (CAD) and finite element analysis (FEA) simulate real-world conditions, allowing engineers to refine designs and preemptively address potential issues, resulting in superior brake hardware.
Finally, sustainability considerations have grown increasingly important. The drum brake forge industry can enhance its expertise and trustworthiness by integrating eco-friendly practices. Using recycled materials, optimizing energy consumption, and adhering to environmental regulations are ways in which companies can demonstrate responsibility and improve their standing with environmentally conscious clients.
In conclusion, the drum brake forge process is a cornerstone of modern automotive manufacturing, requiring a blend of experience, expertise, authoritativeness, and trustworthiness. By focusing on these elements – from material selection through precision machining to rigorous testing and sustainability – manufacturers are able to produce drum brakes that not only meet but exceed industry standards, catering to both current and future demands.